
Timm Delfs ist Publizist und Betreiber eines Fachgeschäfts für ausgefallene Uhren in Basel.
Von Timm Delfs
Omega hat mit dem Eidgenössichen Metrologischen Institut METAS einen neuen Prüfstandard für Armbanduhren erarbeitet, der den bislang meistbenutzten Chronometerstandard COSC ergänzt. Uhren, die den COSC und den neuen Test bestehen, dürfen das Prädikat Master Chronometer auf dem Zifferblatt tragen.
Die vom britischen Uhrmacher und Erfinder George Daniels konstruierte Co-Axial-Hemmung ist mittlerweile in allen Werken der Bieler Manufaktur Standard geworden. Die Hemmung war Ende des 20. Jahrhunderts auf ausdrücklichen Wunsch von Nicolas G. Hayek bei Omega eingeführt worden. Die Anfangsphase war harzig, weil sich die Industrialisierung der Hemmung, die ursprünglich für Taschenuhren ausgelegt war, schwieriger gestaltete als erwartet. Der komplexe Aufbau auf mehreren Niveaus verlangte nach engeren Toleranzen als eine herkömmliche Ankerhemmung. Ausserdem funktionierte das System bei der üblichen Frequenz von 4 Hz (28’800 a/h) nicht zufriedenstellend, weshalb die Ingenieure sie auf unübliche 3,5 Hz (25’200 a/h) senkten. Nachdem in der Anfangsphase Standardwerke für die neue Hemmung umgebaut wurden, erschien im Jahr 2007 das erste hauseigene Automatikwerk, das um die Co-Axial-Hemmung herumkonstruiert worden war, das Kaliber 8500/8501. Damit entwickelte Omega sich immer mehr zu einer wahren Manufaktur mit proprietären Werken, die sich auch optisch ganz klar von den ETA-Standardwerken unterschieden.
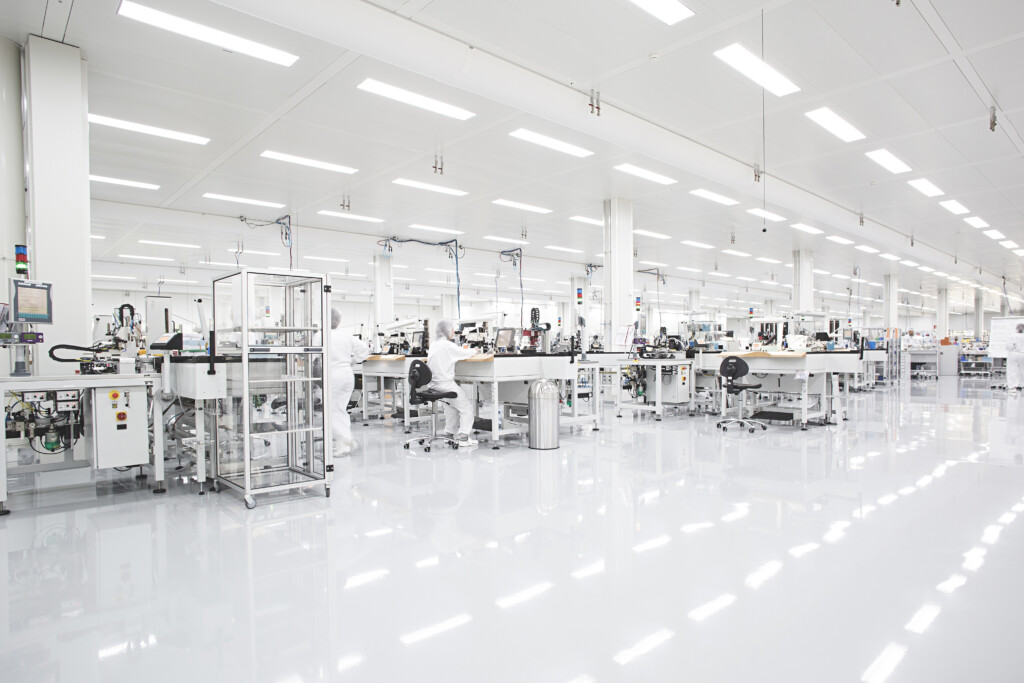
Montagehalle von ETA/Omega in Villeret (Foto Omega)
2009 wurde die mittlerweile ausgereifte Hemmung durch eine Silizium-Spiralfeder ergänzt, was sie gegenüber Magnetfeldern unempfindlicher machte, da der Halbleiter Silizium nicht zu den Metallen zählt und sich nicht magnetisieren lässt. Weitere Vorzüge des Materials, das sonst für die Chipherstellung verwendet wird, liegen in der beinahe absoluten Masshaltigkeit, der Möglichkeit, ganz spezielle Formen zu realisieren, sowie der Herstellung grosser Quantitäten identischer Werkstücke.
Die Produktion eigener Werke bedingte eine Auslagerung aus der ursprünglichen Produktion bei ETA in Grenchen. Dort entstand eine 2013 eröffnete Fertigungsstrasse für die Kaliberfamilie 9300, die mit einem Chronographen ausgestattet ist. In Villeret, gleich neben einem Gebäude des Hemmungslieferanten Nivarox, entstand ein neues, im November 2014 bezogenes Fabrikationsgebäude für alle übrigen Automatikkaliber mit Co-Axial-Technik. Die Produktion geschieht unter Reinraumbedingungen und mit einer intern entwickelten Montagestrasse, die es erlaubt, dass in ein- und demselben Montagefluss unterschiedliche Kaliber montiert werden können. Zu Beginn des Vorgangs wird jede noch nackte Grundplatine in einen Werkhalter aus Kunststoff gesetzt, den sie bis zum Schluss nicht mehr verlässt. Jeder Werkhalter enthält einen Chip mit einer individuellen Adresse, der an jeder Montagestation über eine eingebaute Antenne ausgelesen wird und das Werk identifiziert. Nach jedem Bearbeitungsschritt wird der Chip mit der Information über die Etappe gefüttert. Die ausgeführte Arbeit wird aber auch nach jeder Station sogleich geprüft, und das Ergebnis ebenfalls auf dem Chip festgehalten. Liegt ein Messpunkt ausserhalb der Toleranzgrenze, fährt die Platine zu der Station zurück, die den beanstandeten Schritt ausgeführt hat, ohne die nachfolgenden Platinen zu behindern. Auf ihrem Weg von A nach B verlassen die Werkstücke immer wieder die Hauptstrasse, um zu den Stationen zu gelangen, wo die ihnen zugeordneten Arbeitsschritte in der richtigen Reihenfolge ausgeführt werden. Viele Operationen, wie zum Beispiel das Schmieren der Lagersteine und der Hemmung werden aus Gründen der exakten Wiederholbarkeit von Robotern ausgeführt. Das Ölen übernehmen piezo-elektrische Düsen, ähnlich wie in einem Tintenstrahldrucker, welche Menge und Position absolut exakt einhalten. Trotzdem kann bei der Montage der Werke nicht auf Handarbeit verzichtet werden. Dort, wo Schrauben angezogen werden, kommen jedoch durchs Band elektrische Schrauber mit exakt vordosiertem Drehmoment zum Einsatz, um ausnahmslos optimal angezogene Schrauben zu garantieren.
In den neuen weissen Hallen von Villeret, dem Örtchen, wo auch die zu Montblanc gehörende Minerva steht, arbeiten rund 300 Mitarbeitende. Wie bei einem Neubau zu erwarten, bestehen noch Kapazitätsreserven. Hier werden die übrigen automatischen Kaliber mit Co-Axial-Hemmung zusammengesetzt, deren vierstellige Bezeichnungen mit einer 8 beginnen. Darunter auch die etwas kleineren Automatikwerke für die Ladymatic und die Constellation für Damen.
Resistent gegen stärkste Magnetfelder
Besonders stolz ist man bei Omega jedoch auf einen neuen Industriestandard für mechanische Uhren in Form eines Zertifikats des eidgenössischen Instituts für Metrologie METAS. Das Zertifikat, welches eine Chronometerprüfung durch das Prüfinstitut „Contrôle Officiel Suisse des Chronomètres “ (COSC) voraussetzt, garantiert, dass sowohl die Uhr als auch das nackte Uhrwerk unter dem Einfluss eines 15’000 Gauss starken Magnetfelds einwandfrei laufen und auch danach nicht davon beeinflusst sind. Das entspricht in etwa der Magnetfeldstärke, die im Inneren eines Magnet-Resonanz Tomographen (MRI) erzeugt wird. Der neue Titel lautet „Master Chronometer“. Er ist nicht von Omega geschützt und darf auch von anderen Marken benutzt werden, welche ihre Uhren unter denselben Bedingungen testen wollen.
Um ein Uhrwerk vor Magnetismus zu schützen, gibt es zwei Möglichkeiten: Man kann das Uhrwerk im Inneren des Gehäuses mit einer Art Dose aus Weicheisen ummanteln, welche den Magnetismus wie ein Faraday-Käfig ablenkt und das Werk nicht durchfliessen lässt. Diese Methode versagt aber bei Feldstärken von über 1000 Gauss. Ausserdem lässt sie weder Zifferblätter mit Öffnungen für Datum und dergleichen, noch transparente Böden mit Blick aufs Uhrwerk zu. Omega entschied sich deshalb für die zweite Möglichkeit, nämlich die sensiblen Komponenten aus nicht magnetisierbaren Materialien zu fertigen. Abgesehen von Silizium für Spirale und Hemmungsrad, mussten aber andere amagnetische Legierungen gefunden werden, um beispielsweise die Unruhwelle, die Ankerradwelle, die Federn für die Stossdämpfung und das Ankerrad selbst herzustellen. Diese gehören zu den ganz grossen Geheimnissen der Bieler Marke.
Das Prozedere
Da METAS solcherlei Prüfungen nicht selbst durchführt, sondern lediglich über die Einhaltung der Standards wacht, hat Omega die Prüfapparaturen am Hauptsitz in Biel eingerichtet. Die Installation des tunnelförmigen, anderthalb Tonnen schweren Permanentmagneten im ersten Geschoss war allerdings ein schwieriges Unterfangen. „Wir mussten um den Magneten herum einen Glaskasten bauen, der einen Sicherheitsabstand garantiert. Alles Eisenhaltige, das dem Block zu nahe kommt, wird so stark angezogen, dass man es nicht mehr zurückhalten kann. Einen Schraubenzieher, der daran haftet, bekommt man nicht mehr weg“, erklärt Andreas Hobmeier, der für das Prüflabor verantwortlich ist.
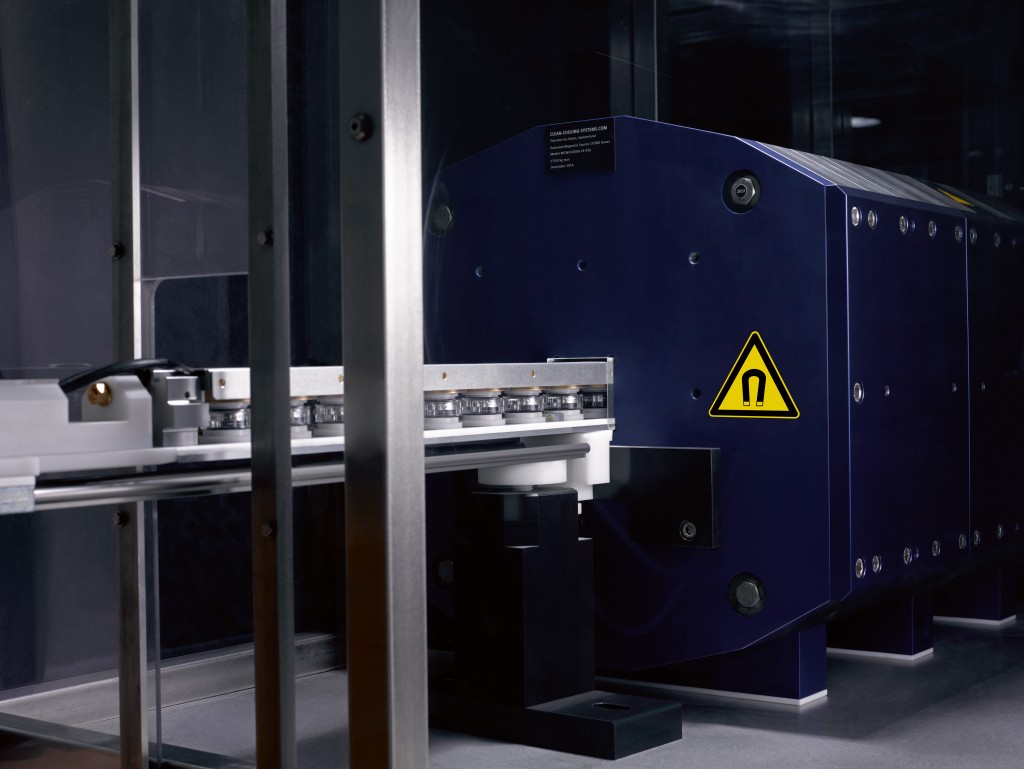
Der erste bei Omega installierte Permanentmagnet mit 15’000 Gauss Magnetfeld. Eine mit 10 Uhren bestückte Schiene ist bereit, in den Tunnel geschoben zu werden. (Foto Omega)
Die Uhrwerke selbst werden geprüft, indem zehn Stück in einer Linie auf einer Schiene befestigt und in die Tunnelöffnung des blau lackierten Magneten geschoben werden. Dort bleiben sie mehrere Minuten, während draussen ihr Gang überwacht und digital festgehalten wird. Nach der Belastung werden die Werke entmagnetisiert, um auch Bauteile wie Schrauben gänzlich von Magnetismus zu befreien, und erneut geprüft. Nachdem die Werke eingeschalt sind, startet das Prozedere erneut. Zusätzlich wird der Gang der Uhren bei 23° und 33° geprüft und jede Uhr auf Wasserdichtigkeit bis zum deklarierten Wert getestet. Die wiederholten Gangprüfungen werden stets in sechs verschiedenen Positionen durchgeführt, die den sechs Flächen eines Würfels entsprechen (Zifferblatt oben, Boden oben, Krone oben, Krone unten, Krone links, Krone rechts). Da die aufwendigen Prüfungen in der Produktion ein Nadelöhr darstellen, soll auch hier in näherer Zukunft die Kapazität vergrössert werden. Wenn Omega den neuen Standard in einigen Jahren auf die gesamte Produktion ausweiten will, dürfte es sich um etwa 700’000 Uhren jährlich handeln. Bis dann sollen mindestens 4 bis 5 Permanentmagnete installiert sein, erklärt Andreas Hobmeier.
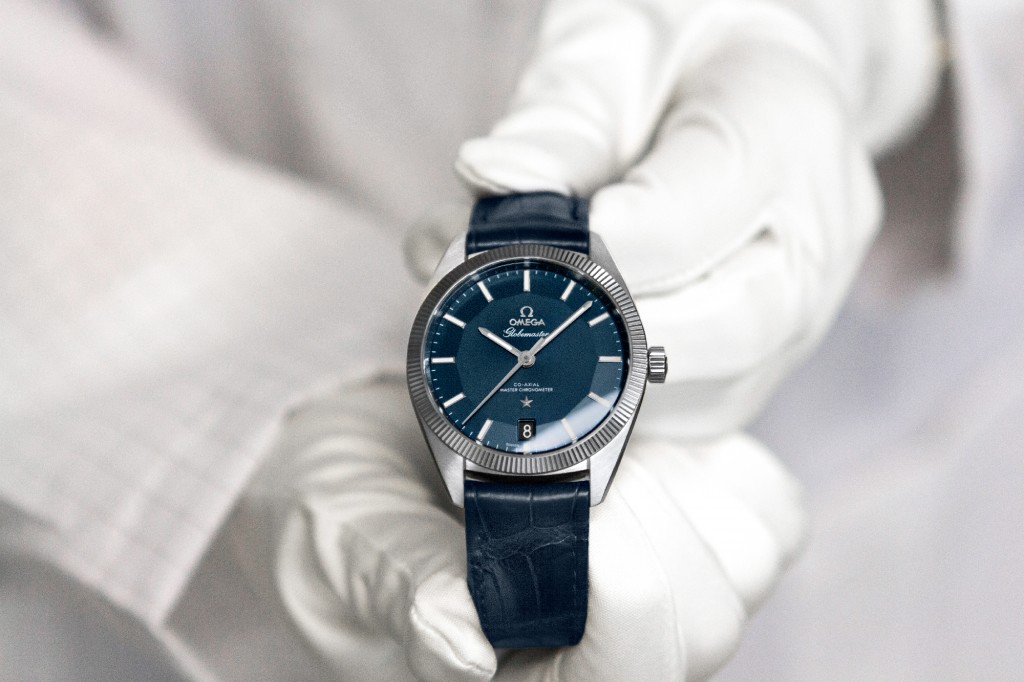
Erste mit dem neuen Zertifikat ausgezeichnete Uhr: eine Globemaster Chronometer. (Foto Omega)
Das erste Uhrenmodell von Omega, welches das Label „Master Chronometer“ auf dem Zifferblatt trägt, ist das an der vergangenen Baselworld vorgestellte Modell Globemaster, dessen Zifferblatt an das ikonische Modell Constellation erinnert, während die kannellierte Lünette eher an ein Konkurrenzprodukt denken lässt. Die ersten zertifizierten Modelle dieser Linie werden vor Ende dieses Jahres ausgeliefert werden.